Mass production of power batteries would be the next trend in the context of the rapid development of the new energy industry. Facing an imbalance between supply and demand in anode and cathode materials of Li-ion batteries, suppliers should work to improve the efficiency of their raw material production and logistics operations.
LEAD established cooperation with Hunan Shinzoom Technology Co., Ltd (hereinafter referred to as Shinzoom) recently. Based on intelligent manufacturing and intelligent logistics, LEAD has provided the company with material warehouse solutions to drive its efficient operations and establish the intelligent brain of modern factories.
The warehouse handling capacity of raw material factory is larger than that of the Li-ion battery industry and single material weight can stand at above 800 kg. The application of traditional half-automatic single-layer warehouses would pose great challenges to warehouse size and labor intensity, severely impeding factory management efficiency. Additionally, Li-ion battery anode and cathode material manufacturers are facing severe dust pollution, which would threaten people’s physical health and prompt short circuit, halt, and AGV road line confusion due to its electrical conductivity.
LEAD customizes the design according to the customer’s site environment and production workflow, helping it to improve the automatic operation and intelligent analysis and decision-making capability of the warehouse system.
Automated stroage and retrieval system design
providing the optimal solution for intelligent warehouse
Based on the strengths of automated stroage and retrieval system and AGVs, Shinzoom has actualized automation in the whole process from raw material input and output, semi-finish product storage and distribution, to final product delivery, noticeably cutting labor costs. Automated storage and retrieval system has improved the height space occupation rate to over 95% and reduced laneway space by 60% with a better layout. LEAD has used its data algorithms to ensure the reliability of warehouse equipment docking while warehouse height, slotting amount and loading weight all reach a record high.
Digital technology upgrade
creating 'intelligent brain of factory’
LEAD applied digital simulation and three-dimensional animation to accurately simulate real work environment at the initial stage of the project, refining strategy design and providing customized planning service to Shinzoom. By taking advantage of big data and cloud computing, the warehouse system can help establish digital management platforms for Shinzoom to collect and analyze key data of each link on a real-time basis. By doing this, comprehensive visual supervision of logistics in factories would be achieved, noticeably improving the efficiency of warehouse management.
Ultra-high protection level
for personnel and equipment safety
The automation of intelligent warehouses has streamlined workforce deployment. Combined with totally-sealed stacker control platforms and laser radar, workers would minimize their exposure to dust pollution and ensure physical health at work. For warehouse equipment, LEAD has applied special protective structure design to reduce the damage of dust to equipment and prevent power failure and machine halt so that factories can maintain smooth operations.
The successful practice of in Shinzoom project will improve the comprehensive layout of intelligent logistics in the upstream and downstream industries of Lithium, play a leading role in the field of new energy, and promote the development of the industry to a more intelligent level.
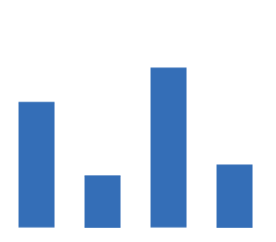